10 técnicas para evitar desperdícios em sua empresa
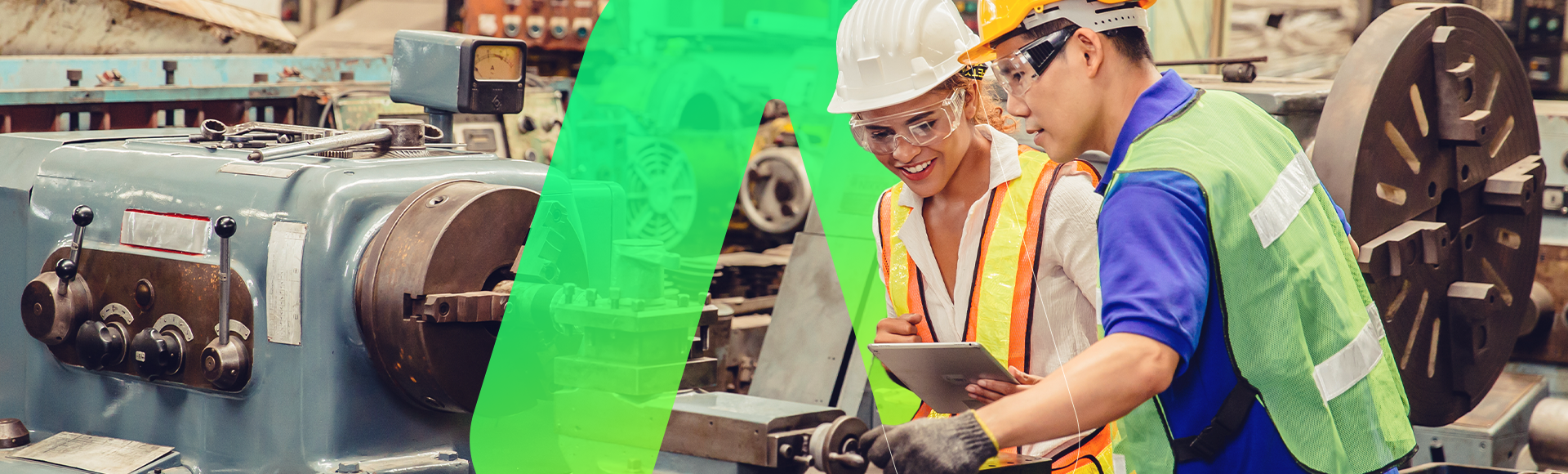
Em um mundo cada vez mais consciente sobre sustentabilidade e eficiência, a minimização de desperdícios tornou-se um imperativo para as empresas. Além dos benefícios ambientais óbvios, a redução de gastos desnecessários também contribui para melhorias significativas na rentabilidade e competitividade das organizações. Seja em termos de recursos financeiros, materiais ou tempo, diminuir os resíduos pode gerar economias significativas e impulsionar a eficiência operacional.
Vamos explorar com profundidade uma questão crítica para as empresas modernas: como evitar desperdícios de maneira eficaz. Aqui, apresentaremos 10 técnicas fundamentais que podem ser aplicadas em diferentes setores e tamanhos de empresas, proporcionando insights práticos e acionáveis para a adoção bem-sucedida de táticas para evitar o desperdiçamento.
A importância da redução de desperdícios em empresas
A abordagem para reduzir o esbanjamento de recursos em empresas, não apenas reflete a responsabilidade ambiental, como também impulsiona a eficiência operacional e a lucratividade. Essa minimização não se trata apenas de evitar o descarte inadequado de resíduos, mas também de otimizar processos, recursos e tempo, garantindo que cada etapa da operação agregue valor tangível.
Case de Estudo: Toyota e o Sistema Lean
Um dos exemplos mais notáveis de uma organização que revolucionou sua abordagem operacional através da minimização de desaproveitamento é a Toyota, com sua filosofia de produção enxuta, também conhecida como Sistema Toyota de Produção. Na década de 1950, a montadora desenvolveu um conjunto inovador de princípios que enfatizavam a eliminação de desperdícios em todas as formas.
O Sistema Toyota de Produção, muitas vezes chamado de “Lean”, foi construído sobre os pilares do just in time e da melhoria contínua. Ao identificar e eliminar estoques excessivos, tempos de espera prolongados e processos ineficientes, a montadora conseguiu, não apenas melhorar drasticamente a qualidade de seus produtos, mas também reduzir custos operacionais substancialmente.
Vamos mostrar técnicas concretas que podem ser aplicadas por empresas de todos os setores, inspirando-se em abordagens como o Sistema Toyota de Produção, a fim de alcançar níveis mais elevados de eficiência, sustentabilidade e competitividade.
Vale destacar que identificar e eliminar gastos desnecessários em empresas requer uma abordagem proativa e sistemática. Inclusive, existem diversas técnicas que podem ser aplicadas para alcançar esse objetivo e otimizar a eficiência operacional.
1 – Mapeamento de Fluxo de Valor (VSM – Value Stream Mapping)
Todo o processo de produção ou prestação de serviços, destacando as etapas e os tempos envolvidos estão visualizados nesta técnica. Isso ajuda a identificar gargalos, atrasos e atividades desnecessárias, permitindo que a empresa planeje melhorias focadas em redução de custos e aumento da eficiência.
2 – 5S
Baseada em cinco princípios japoneses: Seiri (organização), Seiton (ordem), Seiso (limpeza), Seiketsu (padronização) e Shitsuke (disciplina). Esta técnica promove a organização do espaço de trabalho, eliminação de itens não essenciais, melhoria da limpeza e criação de padrões, resultando em uma operação mais eficiente.
3 – Just-in-Time (JIT)
Eliminar o estoque excessivo, reduzindo os custos associados ao armazenamento e ao gerenciamento é a premissa desta técnica que incentiva a produção apenas quando necessário, minimizando perdas de recursos em excesso.
4 – Kaizen
O Kaizen se concentra na melhoria contínua, encorajando os funcionários a identificarem pequenas melhorias diárias em seus processos de trabalho. Essa técnica ajuda a eliminar ineficiências e gastos ao longo do tempo.
5 – Análise Pareto
A análise de Pareto, baseada no Princípio de Pareto (80/20), ajuda a identificar os 20% dos fatores que causam 80% dos problemas. Ao focar nesses fatores críticos, a empresa pode ter resultados mais significativos.
6 – Manutenção Produtiva Total (TPM – Total Productive Maintenance)
Eliminar paradas não programadas, defeitos e perdas de desempenho nas máquinas e equipamentos. A manutenção preventiva e a conscientização da equipe sobre a adoção dessas medidas contribuem para redução de desperdícios.
7 – Análise de causa raiz
Quando problemas recorrentes surgem, a técnica de análise de causa raiz ajuda a identificar a causa subjacente. Também chamada de RCA (root cause analysis), é uma metodologia que, como o próprio nome diz, pretende chegar na raiz do que está causando o problema, identificando as suas reais causas e buscando a resolução.
8 – Benchmarking
Comparar processos e práticas com empresas líderes no setor pode revelar oportunidades de melhorias e inspirar a adoção de práticas mais eficientes.
9 – Tecnologias de automação
A automação de processos repetitivos e manuais pode reduzir erros e acelerar a produção, resultando em uma operação mais eficiente.
10 – Redesign de Processos
Às vezes, é necessário repensar completamente os processos existentes. Por isso, o redesign pode eliminar passos desnecessários e simplificar fluxos de trabalho.
Lembre-se de que a eficácia pode variar dependendo da situação e do contexto de cada empresa, portanto, é importante avaliar cuidadosamente as necessidades e objetivos individuais ao escolher as técnicas a serem implementadas.
Técnica | Complexidade | Tempo de Implantação | Custo de Implantação | Eficácia por Setor |
Mapeamento de Fluxo de Valor | Moderada | Médio | Baixo | Manufatura, Logística, Serviços |
5S | Baixa | Curto | Baixo | Qualquer Setor |
Just-in-Time (JIT) | Alta | Longo | Médio | Manufatura, logística |
Kaizen | Baixa | Curto | Baixo | Qualquer Setor |
Análise Pareto | Baixa | Curto | Baixo | Qualquer Setor |
Manutenção Produtiva Total (TPM) | Alta | Longo | Médio | Manufatura, Indústria |
Análise de Causa Raiz | Moderada | Médio | Baixo | Qualquer Setor |
Benchmarking | Moderada | Médio | Médio | Qualquer Setor |
Tecnologias de Automação | Alta | Médio | Alto | Manufatura, Tecnologia da Informação |
Redesign de Processos | Alta | Longo | Alto | Qualquer Setor |
Ao implementar essas técnicas de forma integrada e contínua, as empresas podem identificar e eliminar desperdícios, resultando em operações mais eficientes, custos reduzidos e, em última análise, em um aumento da competitividade e da sustentabilidade financeira.